More about the technology
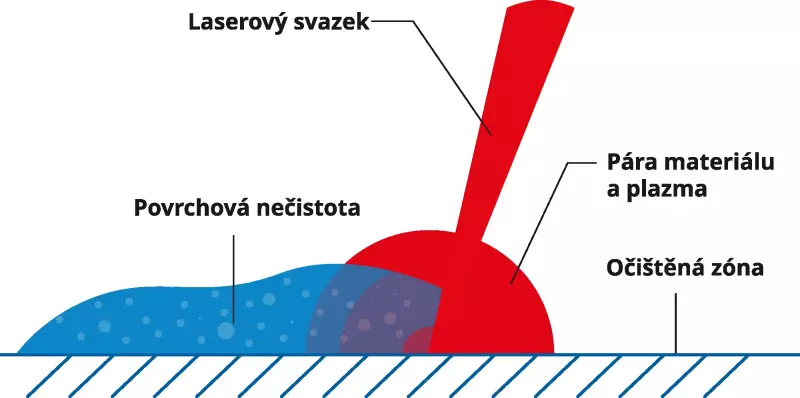
Focused laser beam technology
Laser cleaning works based on the principle of laser ablation which leads to progressive dissociation of the individual molecular bonds which are released from the existing surface.
Highly intensive laser impulses with length of several nanoseconds induce very fast material heating up which consequently evaporates. At the same time local explosions take place, which remove material from the surface.
During laser cleaning almost no waste material is produced because most of the impurities evaporate, due to high efficiency of the laser resonators the laser cleaning process keeps the operating costs very low. In contrast to other methods, all you need for laser cleaning is the connection to 230V/50Hz. Laser cleaning is a non-contact, non-abrasive method which is very gentle to the material surface. Based on the fact that the interaction of laser radiation with material depends on the material it is possible to set the cleaning parameters in order to keep the material surface and structure after cleaning undamaged.
What is the greatest value of our cleaning lasers?
Gentleness
Laser system - if set correctly - does not damage the surface and structure of material cleaned, not in the least. It does not come to unwanted material decrease, nor its thermal deformation. Laser cleaning is suitable for e.g. cleaning objects which are very expensive.
Speed
One of the strongest qualities of laser is that it can be even 5x faster than conventional technologies.
It usually concerns the following applications: removing contamination, oxidation, surface corrosion, paints
Repeatability
Laser is able to reach the same results repeatedly, with help of its own operative system the user can easily select, save and name the individual tasks and parameters for uncomplicated repeated cleaning.
Flexibility
Depending on the needs of the application it is possible to design a laser and integrate it into production line, build a robotic workplace or deliver a precise portable mobile unit for a large scale of applications.
Operating costs
While laser requires a relatively high acquisition costs, its operation is extremely low-cost. Electric energy consumption is in the units of kilowatts (based on the model) so we usually mention in our quotation that one hour of cleaning costs less than 1 EUR/hour. This price already involves protective glass, electric energy and filter change (where filters are necessary). No other laser components need to be changed regularly, the laser operating costs are within these limits.
Lifetime
Lifetime of laser diodes is more than 100 000 operating hours, that is 4166,66 days or 11,41 days of non-nstop operation. The newest sources can even have lifetime up to 200 000 operating hours. Laser source makes 50% price of the entire machine, therefore we highly recommend you to focus on this component, its quality, lifetime and its producer. It is the component where poor quality producers most frequently try to save money on.
Ecology
Very low power and electric current consumption, laser cleaning does not generate too much waste, compared to other methods it does not produce contaminated cleaning medium and emit unadequate noise. This all makes this cleaning method very eco-friendly, sustainable and suitable for application in the 21st century.
Laser is the future
Laser cleaning market value in 2020 was estimated at 580,4 milllon USD and it will expectedly reach 762,2 million USD until 2027.
Our lasers clean and remove
- corrosion and oxidation
- paints and varnishes
- ink
- glues
- polyurethane foams
- mould separators
- fabrics
- carbon
- rubber
- plastic materials
- oils
- grease
- fats
Now we will try to explain what kind of laser operations are possible, what to focus on in particular, how much charge for the work and what eventually does not make sense, or only marginally.
One of the most frequent questions is how much charge for the work, what are the costs for 1 hour of cleaning a particular surface, e.g. for 1 m2.
We advise our clients to calculate laser cleaning as a whole, i.e. contract for work. Based on the fact that laser cleaning can be several times faster and cheaper than traditional technology it usually pointless to charge an hourly rate or according to square meters.
Practical example
Your customer usually cleans his industrial injection moulds mechanically, chemically or with dry ice. Cleaning with the current technology takes 8 hours (he needs to take the mould out, let it cool down, clean it, warm it up, put it back). Furthermore it is necessary to include the costs for cleaning. He will need max. 1 hour to clean everything with laser and usually directly inside the machine. So it does not make much sense to charge for 1 cleaning hour but do it proportionally - make provision also for the fact that the customer has extra 7 hours for work and thus can generate income. If you cannot agree on a contract for work, the rates will be within these limits:
Price for one hour of laserwork
Talking about hourly rate, the most frequent rate is btw. 40 – 140 EUR/hour according to a model and country where the laser is operated and also based on the volume of cleaning hours.
Price per m2
This rate is very individual and there can be really big differences based on the evt. application, i.e. what you need to clean / remove and of course also based on the performance model. Units of meters per hour, or even 10 m2/hour – based on this the price will be calculated.
What to focus on in order to shorten the recovery as much as possible? (this mainly concerns the businesses that want to add laser to their service portfolio or want to start business in this field)
Clean all very expensive, precious, historically valuable, irreparable items. The emphasis is placed on 100% saving properties and dimensions where it is not possible or thinkable to use any mechanical power (wire brush, cutting machine, sanding, ice,…). Laser can be definitely used for many other things but those mentioned below are essential for the fastest recovery possible of lasers: precious automobiles, production moulds for injection or casting, mechanical components, components such as motors, gearboxes, turbines, production lines for gluing, soldering, foam application, vacuum chambers, historical objects - buildings, monuments, bridges, graffiti…